Are you trying to make your third-party logistics (3PL) operations more efficient and profitable? Then understanding the value of warehouse management in 3PL operations is crucial! When broken down into categories, 3PL services can be time-consuming and expensive. Upgrading your current warehouse management system can help you reduce labor costs, save time and make better customer service decisions. But it needs to be implemented correctly! In this article, we’ll go over exactly why warehouse management is so important for 3PL operations. We’ll then summarize various ways to integrate the best systems on the market that enriches your 3PL operations.
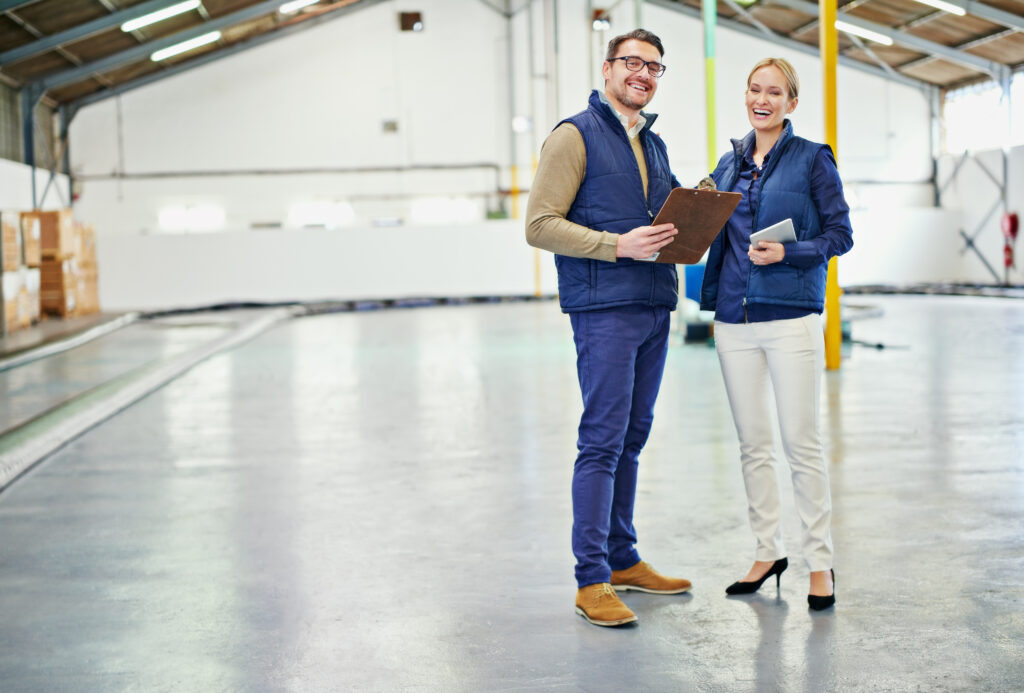
What is the role of Warehouse Management in 3PL Operations?
Warehouse management plays an integral role in 3PL (third-party logistics) operations. It’s responsible for managing the physical inventory in the warehouse, from order processing to delivery. The team of skilled warehouse workers, equipment operators, and warehouse managers collaborate to manage stock levels, update orders, and issue goods to customers in a timely manner. Warehouse management in 3PL operations is essential for the overall success of the operation. In order for 3PL companies to maximize efficiency and profits, warehouse management must be done correctly.
What are the advantages of a good Warehouse Management System?
When you have a good warehouse management system in place, it can provide numerous advantages and make your overall 3PL operations significantly more efficient. A well-managed warehouse can be incredibly valuable to any 3PL business, and here’s why:
1. Improved Tracking
A good WMS allows for tracking of inventory from the moment it arrives at your facility through the end of its life cycle, providing real-time data about stock levels and locations. This ensures that dead stock does not languish in storage and makes it easier to replenish stocks as needed.
2. Increased Accuracy
When a WMS is utilized properly there will be fewer mistakes due to improved data accuracy. This reduces the number of billing or fulfillment errors, resulting in customer satisfaction and fewer returns while allowing you to fulfill orders faster.
3. Reduced Costs
With improved accuracy comes greater savings from reductions in waste and labor costs, resulting in lower overhead expenses for your business. Having a clear view of what’s in stock also helps reduce shrinkage by quickly locating potential theft activities; this helps protect profits and further boost ROI.
4. Enhanced Efficiency
Good warehousing management systems reduce the time required for tasks like data entry, inventory inspections, or search operations by streamlining these processes with automation tools like barcode scanning and RFID tracking. This helps logistics managers react quickly when an order is placed or update delivery times when products encounter delays during transport—all while freeing up resources that would have been used addressing manual tasks instead.
5. Better Customer Service
A good WMS helps to ensure that orders are fulfilled quickly and accurately, resulting in improved customer service. This can lead to increased customer loyalty and repeat business, as customers will be more likely to return if they have had a positive experience with your 3PL operations. Additionally, having a clear view of inventory levels allows you to provide accurate delivery times and better manage customer expectations.
Overall, implementing a warehouse management system is an essential part of having effective 3PL operations; the benefits mentioned above all contribute to better service for customers, more efficient use of resources, and ultimately greater profitability for your business!
How do you optimize your 3PL operations with a quality Warehouse Management System?
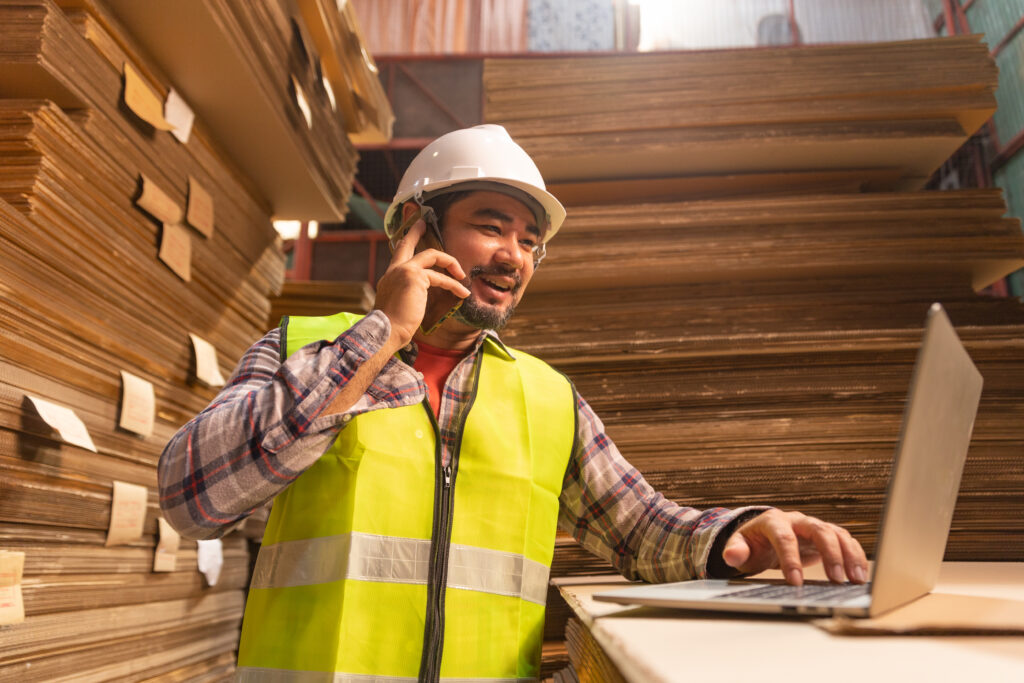
Optimizing your 3PL operations with a quality Warehouse Management System (WMS) is possible. To do this, follow these steps:
1. Evaluate Your Needs and Challenges
The first step to optimizing your 3PL operations with a quality WMS is to evaluate your current needs and challenges. Take the time to assess what processes are currently in place, identify any areas of improvement, and determine what type of system would best meet your needs. Consider factors such as the size of your warehouse, the types of products you handle, and the number of orders you process on a daily basis.
2. Choose the Right System
Once you have identified your needs and challenges, it is time to choose the right WMS for your 3PL operations. Consider features such as inventory management, order fulfillment, shipping and receiving, and customer service capabilities. Make sure that the system you choose is user-friendly and can be easily integrated with your existing systems.
3. Train Your Staff
It is also important to train your staff on how to use the system. Make sure that everyone understands the features and functions of the system and how they can be used to optimize processes and improve customer service.
4. Monitor Performance
After implementing a WMS, you should monitor performance. This will help you identify any areas of improvement and ensure that the system is working as efficiently as possible. Regularly review data such as order fulfillment times, inventory levels, and customer satisfaction ratings to ensure that your 3PL operations are running smoothly.
5. Make Adjustments
If you find that your WMS is not performing as expected, it may be necessary to make adjustments. This could include changing the system settings, adding new features, or even switching to a different system altogether. It is important to stay up-to-date on the latest technology and trends in order to ensure that your 3PL operations are running optimally.
By following these steps, you can optimize your 3PL operations with a quality Warehouse Management System. A WMS can help streamline processes, improve accuracy, and reduce costs. Additionally, it can provide greater visibility into your operations and help you make better decisions. Ultimately, a quality WMS is an invaluable tool for any 3PL operation and can help you maximize efficiency and profitability.
Work with K-5 Solutions!
K-5 Solutions is a 3PL provider with 50+ years of experience and space available. Contact us today to learn more!